Our Team
Knowledge is everything in gas detection. Knowledge about the use of our products, about maintaining and repairing them, about their technical features and limitations.
That’s why 7Solutions makes great effort at training and educating every single employee.
We are ISO-9001 certified, which means we have all our processes documented and available for every staff member. We even have a LEAN/6 Sigma specialist to optimize our processes, so we continue to improve on our – already market leading - service and procurement lead times.
Our staff members are all trained in gas detection practices, along with VCA certification for safe use and maintenance.
What does that mean from a practical point of view?
We don’t let just anyone work on your instruments. Our technicians work under supervision in their first months with the company, taking as much manufacturer’s service training as possible. Every new product is dissected and analyzed to find its peculiarities. Everything we find is documented and used as training base for new – or new to the instrument – staff. Also, we take an extensive inventory of all consumables, sensors, batteries, and other parts that have to be changed in order to guarantee its conformity.
(Fun fact: Every gasket has to be thoroughly checked and replaced if necessary before putting a gas detector back together? Failure to do so voids the Ex/ATEX certificate!)
Every technician is trained for the instrument he or she services. Rigorous quality control means no instrument leaves the department before it’s in as-new condition.
Reassuring thought, isn’t it?
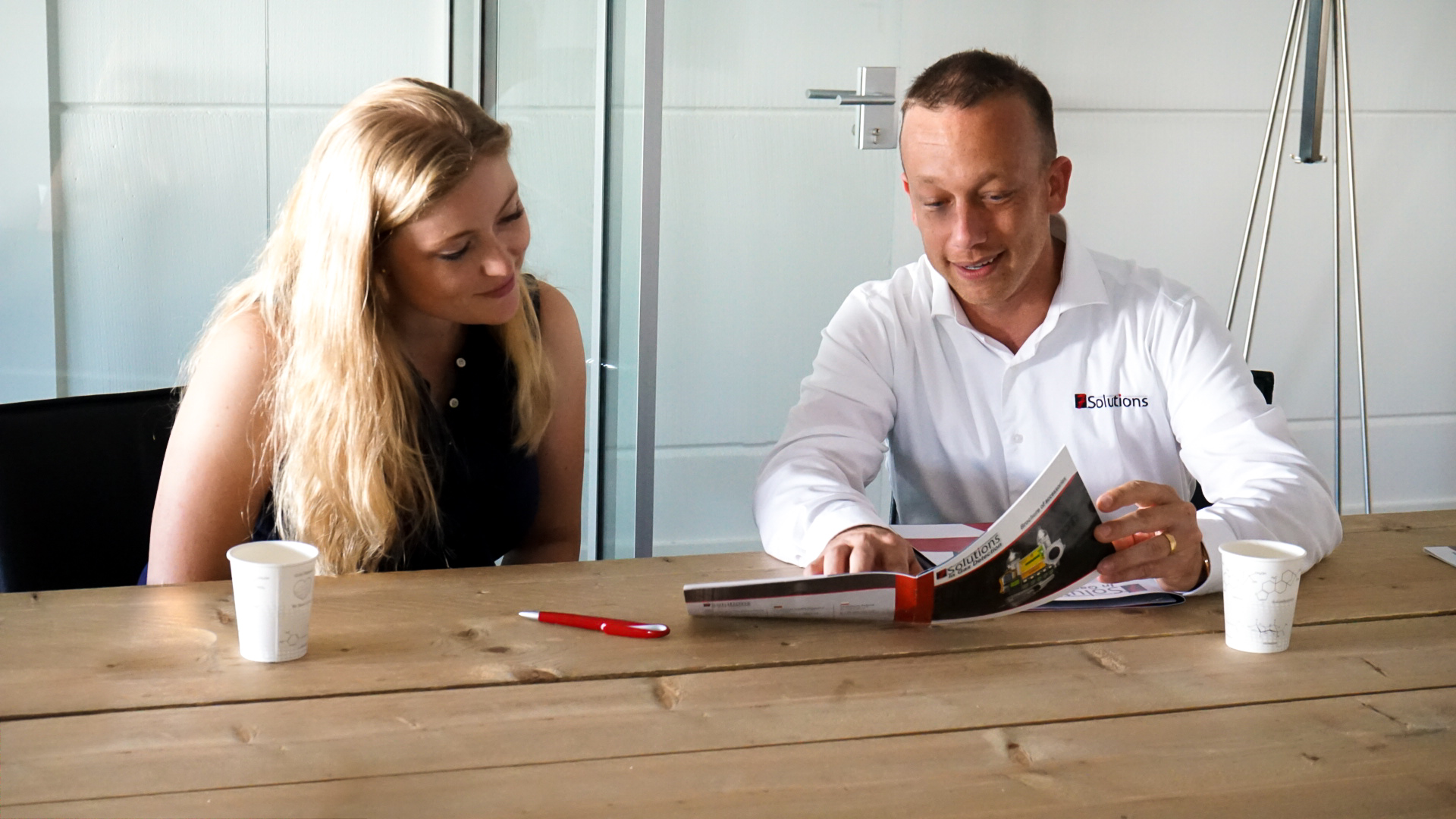
Our team is stand-by and ready to assist you.
Meet some team members
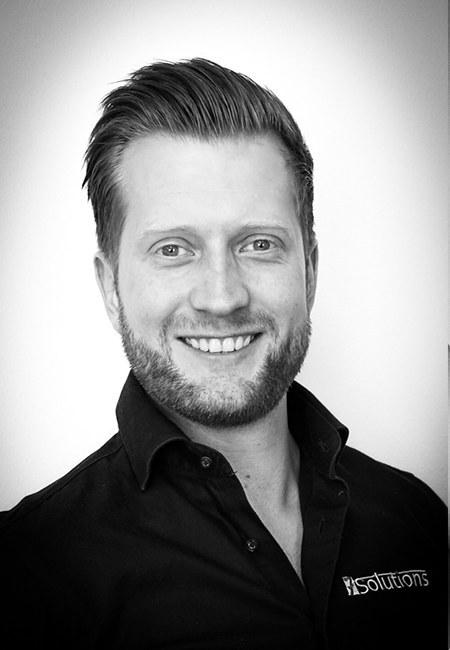
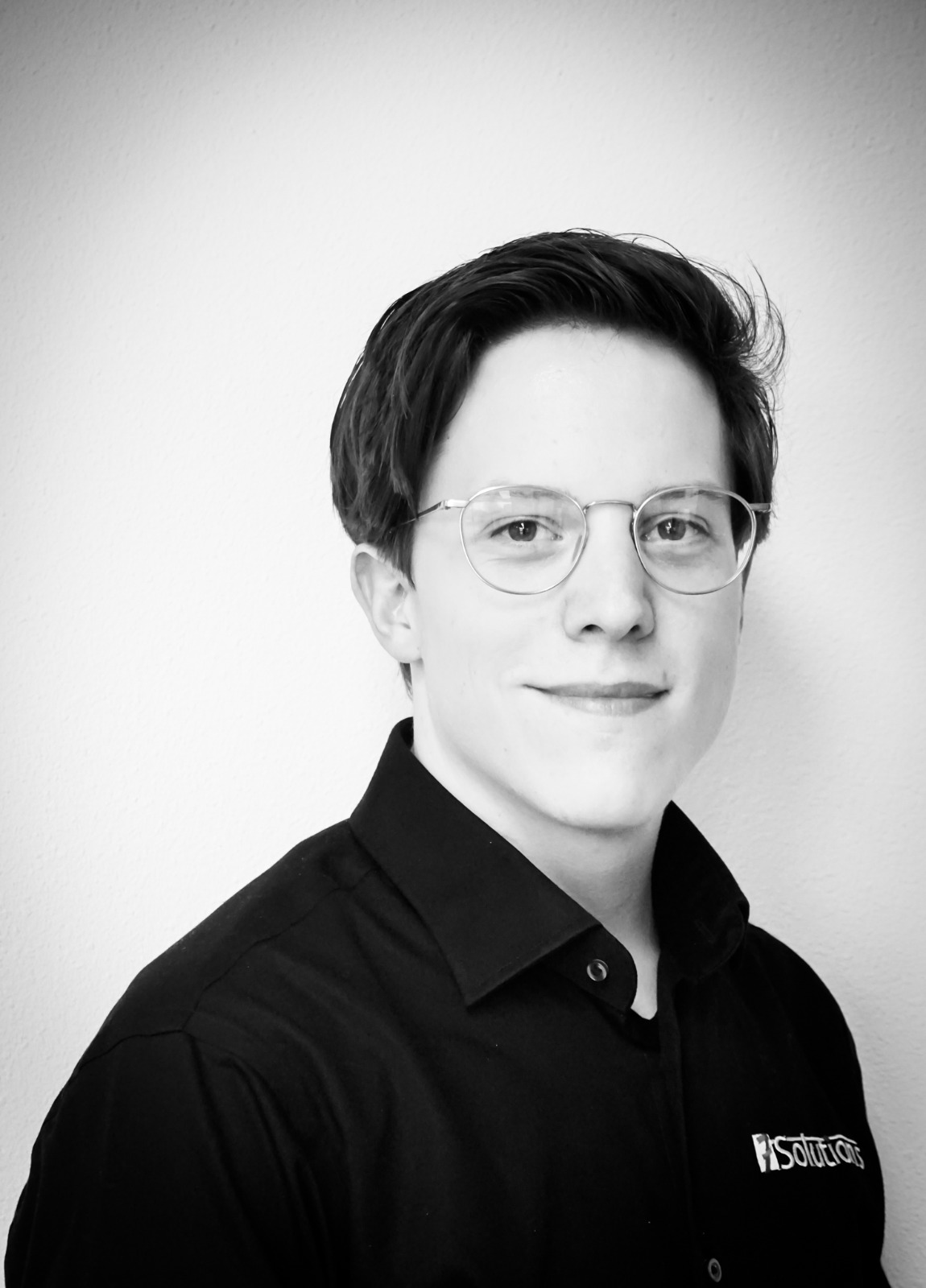
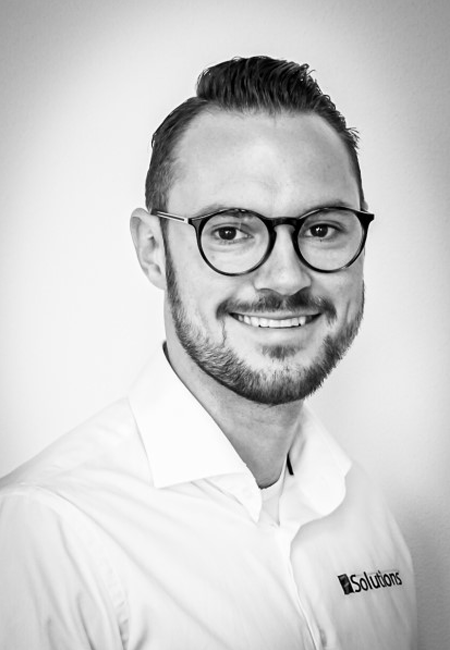
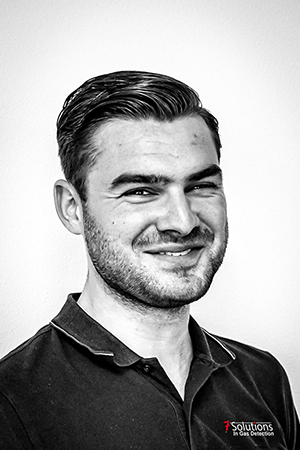
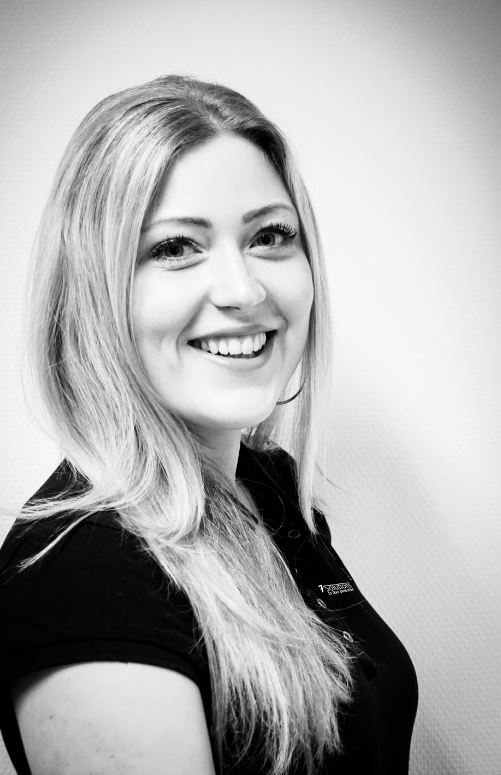
Stay up to date
Optimal tubing and piping materials for gas detection
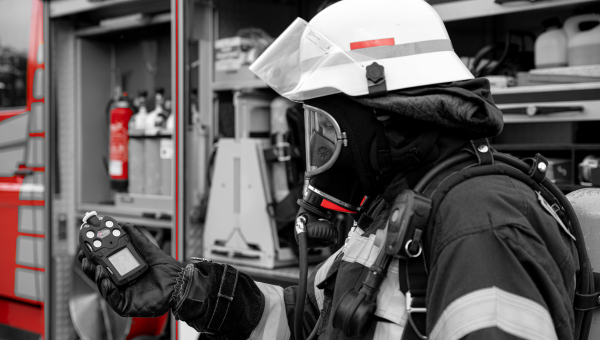